アイリッシュリネンの最高峰 ハードマンズ社のリネン生地は「リネンのロールスロイス」といわれ、最高の品質を誇っていました。今日ハードマンズ社は残っていませんが、ハードマンズの技術と名前が残り今日に伝えられています。そのリネンを織る工程を、フランス・ノルマンディーのフラックス畑から、中国の紡績工場、日本の製織工場と現場を辿ってきました。
リネンの良さを理解するには、リネンがどのように生まれてきたのかを理解する必要があります。
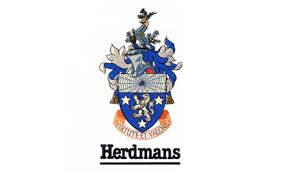
リネン生地が生まれるまで
リネン(麻)の生地が作られるまでにはいくつもの工程がありますが、大きくわけて
- 1.フラックス草(リネン糸の原料)を育て、収穫する
- 2.フラックスからリネン糸の原料を取りだし、スライバーを作り紡績する
- 3.紡績した糸で布を製織する
この3工程に分けられます。
1 フラックス草を植える
リネンの原料となるフラックス草は高さが80~120cmになる草です。もともとはエジプトが原産地といわれますが、比較的涼しい地域での栽培に適しています。
ヨーロッパのフラックスはほとんどがフランス・ベルギー
現在、最も多く栽培され、品質が高いのが北フランス・ノルマンディー地方~ベルギー~オランダの地域で栽培されるフラックスです。ヨーロッパのフラックス(リネン)のほとんどが、この地域で栽培されており、さらにその80%は紡績のために中国へ輸出されます。
一般に フレンチリネン、ベルギーリネンと呼ばれるのは、この栽培地域のことを指しますが、世界のフラックスの8割がこの地域で栽培され、さらに8割はフランス産なので、フランス産は全世界の6割以上のシェアを誇ります。ですので、産地名は正直あまり意味はありません。リネンは連作が無理で、土地の力を奪うために6年サイクルで栽培されます。後の期間は、小麦やトウモロコシ、ジャガイモなどが植えられます。つまり、急激に栽培を増やすことはできない繊維といえるでしょう。
一週間しか咲かないリネンの花
6月になると、青い可憐な花を咲かせます。この花の開花は一週間しかないので、なかなか出会えないといいます。2014年にノルマンディーを訪れたときは幸いにこの開花に出会うことができました。
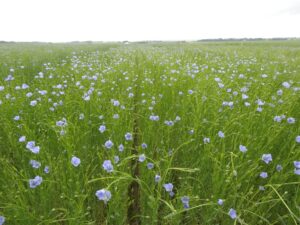
7月になると実がなり、刈り取りが行われます(厳密には引き抜くのだそうです)。刈り取られたフラックス草はそのまま1月~1月半ほどそのまま地面に置いたままにするのです。リネンの繊維は中から取り出すので、表皮を乾燥させて取り出しやすいようにするためです。
乾燥を終えたフラックス草は、丸められてこのように保管されます。実は栽培時に、良い畑かどうか、生育状況はどうかがチェックされて、フラックスの出来の良し悪しをチェックしているのだそうです。これが、リネン糸の良し悪しに大きく関わってきます。
2 リネン糸を紡績する
2-A スカッチング
乾燥したフラックス草の中心部にある繊維を取り出す工程がスカッチングです。丸巻にされたフラックスを解体し、表面の不要な部分を削り取って行きます。
下の画像は2014年 ノルマンディーのTerre de Linの工場
天然繊維なので、当然ながら品質に優劣があります。この段階では10段階で分けられ、同じように丸巻にされますが、大きくはファーストものとセカンドものに分けられます。セカンドは繊維長が短く良いリネン糸は得られません。ほとんどのフラックス原料はこの段階で出荷されます。場合によっては次の行程のハックリングを行って、スライバーという状態まで加工が行われます。
この行程は、実際に訪れたTerre de linのビデオをご覧ください。
2-B ハックリング 繊維を梳く
ここからは紡績工場です。入荷したフラックス原料を解体し、ハックリングの機械にかけます。ハックリングとは、いわば汚れている繊維を櫛で何回も梳く行程です。これにより、短い繊維や不純物などを取り除きます。
ハードマンズのリネン糸を扱う 上海柳川大橋麻業 提携の 湖州金博亜麻紡織有限公司の工場へ2018.9訪れました。
この上の画像の下に貯まっているのは、ハックリングによって出たフラックスのゴミですが、これは捨てられるのでは無く、しばしば短繊維のセカンドの原料と一緒に混ぜて再利用されます。もちろん、そのような原料では細番手の糸は紡ぐことができません。
2-C スライバーを作る
スライバーは粗紡糸の元になります。ハックリングされたフラックス繊維を順番に繋げていく行程です。良いものは2枚目の画像のように、ムラのある上下の端は再度梳いて、不要なものを取り除きます。この行程がいい加減だと、ネップなど風合いを損ねる要因となります。
スライバー行程は何度となく繰り返され(2~4回)、粗紡糸が作られます。多くの紡績メーカーでは、この繰り返しの行程で、品質の劣るスライバー等を混ぜて使うので、通常この行程は見せてもらえないそうです。今回(2018.9)見せていただけたのは、本物を使っている、ごまかしはしていないという証でもあります。
2-D 精錬して粗紡糸を作る
精錬はスライバーに含まれるゴミやペクチンなどを取り除く作業です。この精錬は本当の職人仕事で、スライバーの状況や温度や湿度などで処理時間を瞬時に決めていくそうです。これは本当のヒミツということで、見せてはいただけませんでした。この行程で、紡績するための粗紡糸を得ることができます。
リネンは亜麻色というシルバーグレー色ですが、精錬と同時に漂白をすることで、白の糸を得ることができます。きれいに染めるためには、ちゃんと漂白するだけでなく、良い精錬のレベルと、スライバー段階の繊維の品質が影響します。
ハックリングが終了した段階で漂白と染色をおこなった糸をトップ糸といいますが、乾式紡績のため風合いは劣りますが、表情のある糸を得ることができます。
2-E 湿式紡績で糸を紡ぐ
粗紡糸から、繊維に撚りをかけて糸を生み出す行程が紡績です。リネンは乾式紡績と湿式紡績の2種類があり、良質なものは湿式紡績(潤紡)からのみ得られます。
上の画像は左が乾式紡績、右が湿式紡績であすが、あきらかに湿式紡績の方が毛羽が少ないことがわかります。アイリッシュリネンは湿式紡績の技術からうまれました。
紡績に使う機械そのものには、大きな差はありません。この工場は中国ですが、厳選されたフラックスを使い、手を抜かない丁寧な行程をすることによって、アイリッシュリネンのロールスロイスとも云われたハードマンズ社から名前を使うことを許されているのです。
このようにして、リネン糸が生まれます。アイリッシュリネンとは、アイルランドで織ったリネン生地、あるいは、アイルランドで紡績したリネン糸という意味がありますが、今日、アイルランドにはリネンの畑も紡績の工場もありません。アイルランドで製織すれば確かにアイリッシュリネンには違いありませんが、糸が悪ければその名にふさわしい品質とはいえません。私たちはアイリッシュリネンの伝統を誇るハードマンズ社の技術を使い、しかも60番手以上の上質な細番手の糸を使って生まれた生地をアイリッシュリネンと呼んでいます。
3 リネンの布を製織する
リネン糸を使って布を織るのことを製織するといいます。この製織は正直どこでも織ることが出来るわけですが、当然製織に関してのノウハウがないと、細番手の布を織ることができません。
3-A 経糸を整経する
最初に経糸を用意します。通常、製織の巾はインチで表されます。今回の当店オリジナルアイリッシュリネン80の場合は75インチなので、経糸は全部で4918本用意する必要があります。さらに、経糸は製織時に上下に動くので、60℃で水溶する水溶性ビニロンを巻いて補強します。今回は28デニールのビニロンをS・Z両方向に二重に巻いています。麻の糸は細番手になればなるほど切れやすいので、十分な注意が必要です。その点合成繊維は非常に楽です。
このようにドラムに経糸を巻いていくわけですが、順番にならばないと後でトラブルになります。
3-B 経糸を織機にかける
次に大変なのが、このドラムを織機にかけて、4918本の糸を間違えなく織機に通さなければなりません。生地を織るというのは、この地味な作業なくしては成り立たないのです。緯糸を変えることは、そう難しくはありませんが、経糸を変えると云うことは非常に手間がかかります。生地巾によりますが、経糸の載せ替えは1日~1日半は最低かかるのだそうです。
3-C 製織する
ここでようやく製織にかかります。緯糸はビニロンでの補強はありません。湿気がないと糸に弾力性が失われて、糸切れが起こりやすくなります。麻は糸切れしやすいために、綿やポリエステルに比べるとスピードを上げにくく効率の良い製織がしにくいのです。今回のような夏の高湿度の場合は不要ですが、涼しくなってくると、部屋全体にスチームを入れて湿度を確保し糸切れを防ぎます。
これはリトアニアのSiulas社の工場です。9月ですが、ヨーロッパは乾燥しているために、織機の部屋はスチームでもうもうとしています。
3-D 仕上げ
75インチで織り上がったリネンの布は約190cm(75×2.54cm)ほどの巾があります。この織り上がった状態の生地を生機(きばた)といいます。この状態ではパリパリと硬いきじです。
この生地をお湯で洗ってビニロンを溶かし、さまざまな後加工を行って、出荷できる布に仕上げます。この過程で横が大きく縮みます。今回は余裕をもって160cm巾に仕上げるために広めに織ってもらいました。この仕上げ工程にも技術の良し悪しがはっきりでます。
地元滋賀県の大長さんの麻の仕上げはさすがといわれる高品質な仕上げです。
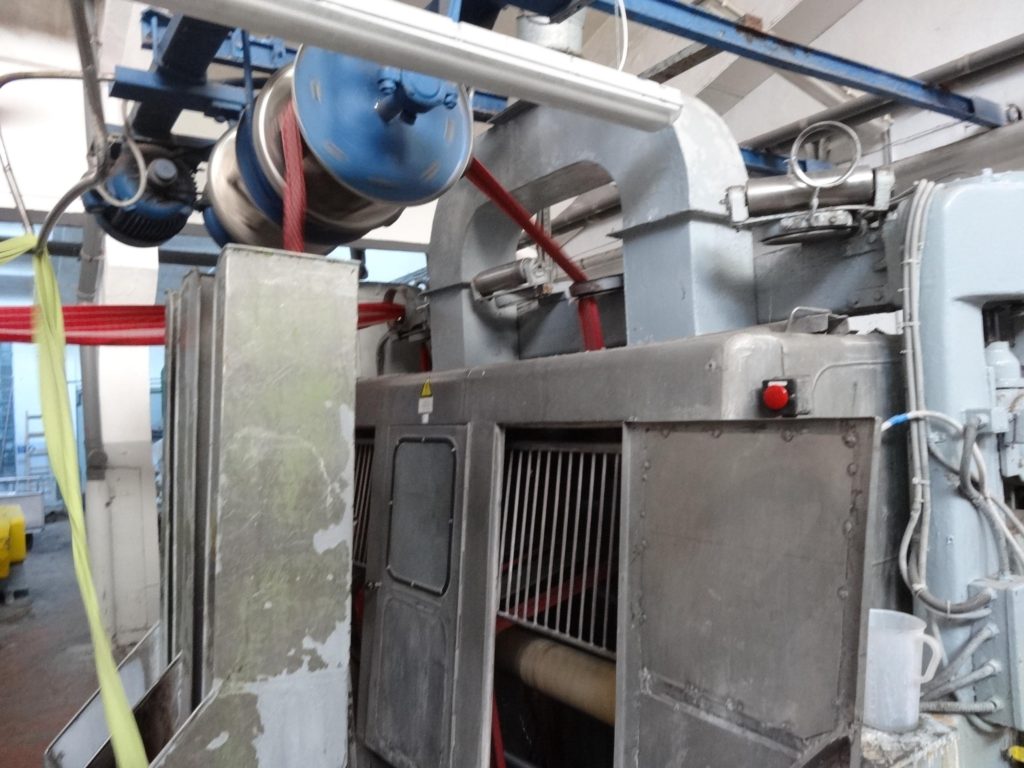
リトアニアのSiulas社の仕上げ工程
仕上げでは、漂白したり、逆に染色したりします。また、CC加工やエアータンブラー加工などのソフト加工も行います。このようにして、ようやく生地に仕上がるのです。
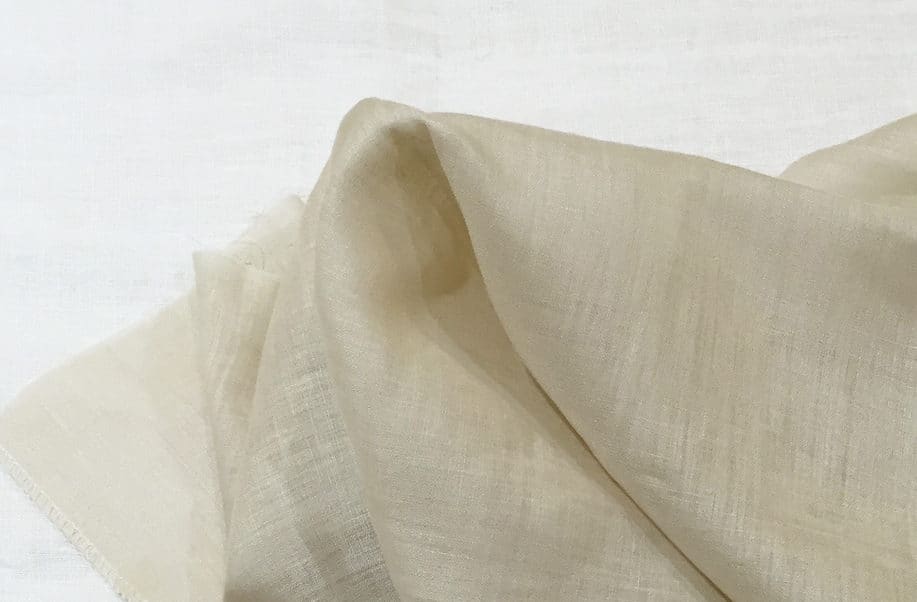
ハードマンズ アイリッシュリネン100 オリジナル シャンパンゴールド染め